Table Of Content

Too often, mistakes in a design are repeated by replicating a previous design. 3D printing is another area that requires the attention of DFM engineers before designs go to production. Design for manufacturing vs design for assembly is an important distinction to make for engineers working in this field. While the differences are subtle, it is good to be aware of them as these two techniques diverge quite a bit when you look at the details. This article discusses various aspects of design for manufacturing and places a lot of emphasis on the role of DFM analysis experts in achieving its goals.
Will I save money with DFM practices?
DFM will have all the stakeholders involved in product development come together and solve problems directly related to the product design, its processes, and the manufacturing process. This ensures a smooth transition of the product from design to assembly up to the mass production level. A full DFM review can also determine if the board can be efficiently produced by a given manufacturer according to the manufacturer’s specific manufacturing capabilities and constraints. For a product's development to be a success, the design and production teams must work together.
Quality
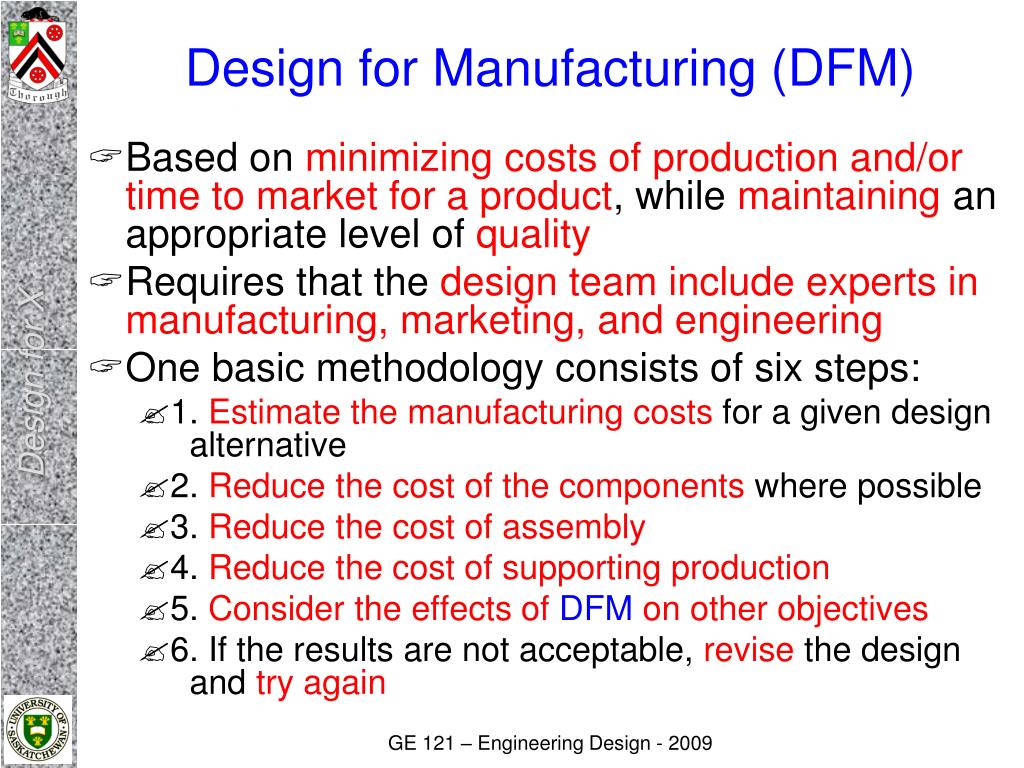
CAD tools analyze material choices, part orientation, tooling needs, and production tolerances to include DFM concepts. Furthermore, CAD models can be translated into machine instructions for CNC (Computer Numerical Control) mills and 3D printers using computer-aided manufacturing (CAM) software. This enables virtual testing and process optimization of manufacturing procedures before the start of actual production. An effective Design for Manufacturability process ensures that when the time comes to increase production levels the manufacturing setup is easy to scale up. Due to in-depth planning of the manufacturing process, the manufacturing companies and/or the contract manufacturer are clear on the deliverables, leading to a smooth production setup. For instance, instead of depending on the manufacturer to calculate the cartesian coordinates for CNC machining, the coordinates for all features can be shown in detail on drawings.
Closing the design-to-manufacturing gap for optical devices - MIT News
Closing the design-to-manufacturing gap for optical devices.
Posted: Wed, 13 Dec 2023 08:00:00 GMT [source]
What Is DFM?
Material selection has a significant impact on DFM results because different materials have distinct qualities that can be important during design and production . For example, Carbon Fiber-Reinforced Polymers (CFRP) and other lightweight, high-strength composite materials have many potential aircraft uses. Engineers can use them to improve structural integrity, reduce weight and increase fuel economy. Leaders who prioritize DFM and allocate the necessary resources to the process are more likely to see positive results. Additionally, leaders who encourage communication and collaboration between design and manufacturing teams can help to break down silos and promote a culture of teamwork. Designing for maintainability involves considering the ease of maintenance and repair during the design phase.
One of the company’s parts was returning all no-bids so they decided to analyze it using aPriori.aPriori showed an almost impossible undercut in the routing. This design feature ended up being a largely arbitrary choice and eliminating it reduced cost by over 50%. The new design was not only far more cost-effective but drew many more bids from potential suppliers.

We outline some of the most important foundational concepts of design for manufacturability below. LEAD provides custom metal parts, plastic parts, and prototype manufacturing services for everyone to quickly prototype, produce, and iterate their products. Any engineer worth their salt is going to also take a very close look at the tolerances specified in the part’s drawings. Tolerance is the total amount a specific dimension is allowed to vary, and manufacturers often receive drawings from customers with unreasonably tight tolerances that can wreak havoc on an RFQ. Design for manufacturability also focuses on using as many standardized parts as possible. Standardized components can be fasteners (nuts, bolts), sealing devices (o-rings, gaskets), and motion mechanisms (lead screws), each of which is easily available directly off the shelf.
Advancements in DFM Techniques and Technologies
It is imperative that the company finalises the manufacturing processes as soon as possible as the remaining four factors are highly dependant on it. The product design may suggest multiple options for manufacturing processes. Each of these choices must be analyzed using DFM principles for an optimum selection. The overall viability must be used as a deciding factor instead of the manufacturing cost. It may be that a manufacturing process has a low production cost compared to another but the overall costs may rack up significantly during distribution etc. Design for Manufacturability is a product design ideology that focuses on creating a better design at a lower cost by optimising the selection of materials and manufacturing processes.
Automating processes can improve efficiency, decrease labor costs, and enhance quality. It strengthens your ability to save money, improve quality, and increase speed. DFM optimizes the design of a product to make it easier and more cost-effective to manufacture. It should begin during the early conceptual design stage of product development. Innovation has accelerated the pace of electronics manufacturing exponentially and profit margins are smaller than ever before.
How Does Design for Manufacturing Contribute to Product Innovation and Efficiency?
By considering manufacturability from the initial stages of design, companies can significantly reduce production costs, improve product quality, and shorten time to market. DFM also helps in identifying potential manufacturing issues early in the design process, allowing for timely modifications and improvements. Furthermore, it fosters better communication and collaboration between design and manufacturing teams, leading to more efficient and effective product development processes. Design for manufacturability or design for manufacturing (DFM) is the engineering practice of designing products to optimize their manufacturing ease and production cost given form, fit, and function requirements. It involves streamlining design elements to facilitate efficient production, minimizing complexity, and optimizing materials and processes. Often interchangeably referred to as design for manufacturing and assembly (DFMA), DFM integrates principles of both manufacturability and assembly into the product design phase.
The following chart offers an excellent visual representation of the effect of an early DFM. As the design progresses through the product life cycle, changes become more expensive, as well as more difficult to implement. Early DFM allows design changes to be executed quickly, at the least expensive location. It may be more or less depending upon the complexity of the design and DFM analysis. The length of DFM varies from project to project depending on a variety of factors. Effective project management and experienced teams can help streamline the DFM process and minimize delays.
This approach often focuses on principles like minimizing the total number of parts used, ensuring that parts are easily insertable, and confining assembly requirements to simple, repetitive motions. Manufacturability describes the degree to which a product can be effectively manufactured given its design, cost, and distribution requirements. We will go through everything about design for manufacturability, including its concept, principles, benefits, and applications in the below article.
Reliability engineers have many other tools and only use the ones appropriate for a particular case. Engineering companies must integrate DFM in the early stages of their design process. Making design changes later can be extremely difficult and come with a hefty price tag, especially when different tooling is needed for the new design. Manufacturability evaluations must be carried out in the early stages as thoroughly as possible.
To realize the full value of the insight provided by your DFM software, the final ingredient is a culture shift toward a cost-conscious, sustainable product engineering culture. Engineers are trained to think about functionality and reliability first, and design-stage manufacturability modeling represents an added analytical complexity. A willingness to re-think a product from the ground-up is an essential element for generating the most impactful estimate. Today, powerful new software tools for DFM analysis have allowed organizations to bring a far more comprehensive understanding of manufacturability and sustainability issues into their design process. A thorough DFM examination of the present design and production practices should reveal several opportunities for improvement.
No comments:
Post a Comment